The environmental impact of rubber compounds
Polymer compounds, such as rubber and plastics, are semi-finished products and can be seen as homogenous mixtures of different ingredients that have previously been designed in a specific formulation or recipe. These ingredients, or raw materials, can be subdivided into the following main categories: polymers, fillers, plasticisers, accelerators, crosslinking agents and many other special products. Only the right composition and a perfect mixing process result into optimum properties of the final product.
The rubber and plastic polymers used in HEXPOL interact with the environment in a number of ways. A certain amount of impact occurs at our units, while other impacts occur during production of raw materials, transports and disposal of the waste that occurs in various places. The environmental impact – in a life-cycle perspective – of polymers is shortly described below.
Synthetic rubber
About 60 percent of world production of synthetic rubber is used for tire manufacture. HEXPOL’s rubber product portfolio contains around 84 percent synthetic rubber, the remainder being natural rubber. Synthetic rubber is a product of the petroleum industry and our experience is spread over a large number of polymer types, for example, EPDM, SBR and NBR.
The environmental impact from the production and use of synthetic rubber derives primarily from energy consumption, use of fossil raw materials, emissions to air and water, and waste products. The positive environmental aspects of synthetic rubber is, for example, associated with products that contribute to energy saving and reduction of noise and vibration.
Natural rubber
The rubber tree Hevea brasiliensis requires a tropical climate. Today, more than 90 percent of all natural rubber comes from South-east Asia, although there are also plantations in South America and Africa. Nearly 70 percent of natural rubber production is used in the tire industry.
An overview of the production process for natural rubber shows that the environmental impact are associated with clearing of forest, the use of energy, chemicals, nutrients and biocides, and from emissions to water. HEXPOL has no rubber plantations of its own and natural rubber makes up around 16 percent of the total use of rubber polymers and around 11 percent of the total use of polymers.
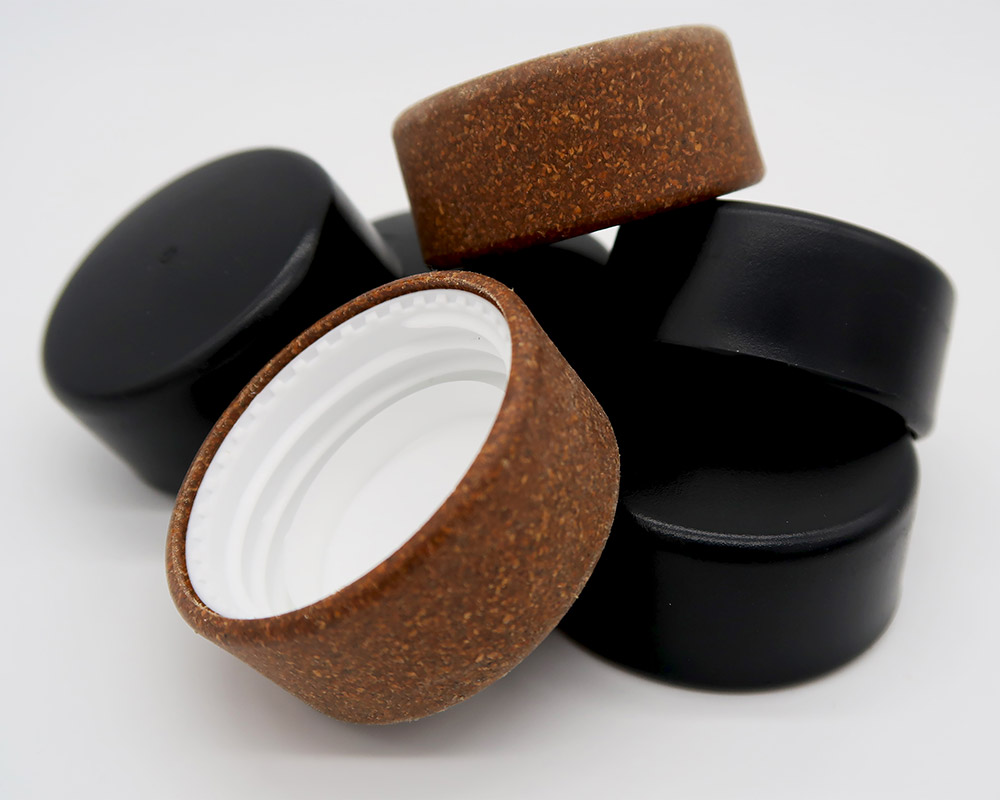
Thermoplastic Elastomers
Thermoplastic elastomers (TPEs) are a family of rubber like materials that combine the performance of thermoset rubbers with the processing ease of plastics, to deliver enhanced design possibilities for a diverse range of markets including household, automotive, industrial, medical, construction, electronics, sports, toys and caps and closures. One thing that TPEs materials have in common is that they are completely recyclable. TPEs can also be combined with natural materials, for example, cork.
Thermoplastics
A thermoplastic is a plastic material that can be repeatedly softened by heating and hardened by cooling. Examples of thermoplastics include polythene (polyethylene), polypropylene and polyamide nylon. Thermoplastics are fully recyclable and in ideal situations thermoplastics can be repeatedly melted and remoulded into new products.
Conventional thermoplastics are produced from fossil petroleum products and the main environmental aspects are the use of non-renewable raw materials, emissions of climate-changing gases and generation of waste. In recent years composite materials have been obtained from the combination of recycled thermoplastics and biodegradable waste of little economic value, for example, rice husks and recycled cotton. Life-cycle analyses show that such composites exhibit a significantly reduced environmental impact during the materials acquisition and processing
phases compared to conventional virgin thermoplastics.